Metal Injection Molding
At Augustine Die & Mold, Inc. (ADM), we specialize in full-service custom Metal Injection Molding of single-cavity and multicavity molds for customers seeking high-volume, high-quality, cost-effective metal injection molded parts made with a wide variety of metal feedstocks including stainless steel, tool steels, copper, tungsten, and more.
The ADM Approach
- Our team will work closely with you from your concept drawing or design to your completed metal injection molded part to ensure that it is manufactured in the most cost-effective way to achieve your end-use goals.
- Leveraging our extensive experience, we injection mold metal parts with complex designs and tight tolerances of +/-0.3% that adhere to the strictest specifications, standards, and compliance requirements of a wide array of industries.
- We guarantee that your finished injection molded metal part will meet the precision and performance requirements matched to its unique application through the integration of scientific methods, analytical software tools, and molding press technologies.
- We are committed to achieving Customer, Regulatory, and Statutory Requirements and customer satisfaction by continually improving our organization and the on-time delivery of innovative, cost-effective products and services of the highest quality and reliability.
ADM's Core Metal Injection Molding Services
- CAD
- Product Design Assistance
- Design for Manufacturability (DfM) Feedback
- Material Selection and Validation
- Prototyping
- Metal Injection Molding
- Quality Inspections
- Value-Added Secondary Operations
Streamlining manufacturing processes from concept to completion through expert insight and in-house capabilities
ADM's Expertise, Your Assurance
Product Design Assistance and Design for Manufacturability (DfM) Feedback
To ensure that your metal part will meet your needs and is cost-effective and cost-efficient to manufacture, we provide product design assistance and Design for Manufacturability (DfM) feedback regarding processing, tooling, and visual and functional applications using the latest state-of-the-art 3D computer-aided design (CAD) and programming software.
Material Selection and Validation
We leverage our vast knowledge of exotic and common metals and work directly with you to determine the best material for your product and its applications.
Prototyping
We facilitate small-volume R&D design and prototyping at low cost before higher-volume production. Our prototyping services assure that your design will meet your requirements for form, fit, and function prior to manufacturing the injection molds.
Metal Injection Molding
We support a wide range of industries with our state-of-the-art 110-ton metal injection molding press with 1.9-ounce, 2.7-ounce, and 3.7-ounce shot sizes working with single-cavity and multicavity molds.
Quality Inspections
We perform strict quality inspection checks throughout your entire metal injecting molding project from the first-article inspection, through in-process production, to the final part.
Value-Added Secondary Operations
We offer and manage a multitude of value-added secondary operations in house as part of your injection molding program, which provides the value of assured quality, improved efficiencies, and overall cost savings. Our secondary operations include:
- Post-processing operations in our high-precision machine shop
- Ink pad printing
- Labeling
- Heat treating
- Plating
- Anodizing
- Debinding
- Sintering
- Machining
- Product assembly
- Packaging
- Warehousing
- Shipping
The ADM Advantage
- What Most Mold Shops Cannot Match: In-House Injection Molding Operations for Custom Metal Injection Molding: Having in-house collaborative personnel who thoroughly understand the highly interdependent processes of mold building and injection molding, along with state-of-the-art equipment, enables us to provide what most companies cannot — a true one-stop shop for precision injection molded parts.
- AS9100:2016 Rev. D Certification | ISO 9001:2015 Certification
- Historically Underutilized Business Zone (HUBZone) Small Business Concern Certification
- International Traffic in Arms Regulations (ITAR) Registration
- Metal Injection Molding key staff with median tenure of 15+ years
- In-house Tool & Mold Manufacturing key staff with median tenure of 30+ years
- Certified Lead Auditor/Quality Systems Manager with 40+ years of experience in Quality Systems
- Mitigation and resolution of poor-performing molding programs transferred to us by OEMs due to poor quality, high prices, or long lead times
- State-of-the-art integrated real-time manufacturing ERP software for increased efficiency and turnaround of production, data collection, troubleshooting, and overall organizational and customer communication
- 221,000-square-foot facility encompassing production and two large warehouses for raw materials, finished products, and lease space for customers with multiple loading docks for efficient pickups and deliveries
- Conveniently located just off the Pennsylvania Turnpike (I-70/I-76) Somerset Interchange Exit 110 and just off US-219 in the Somerset Industrial Park in Somerset, Pennsylvania
- 24/7 operations capability to meet customers’ demands
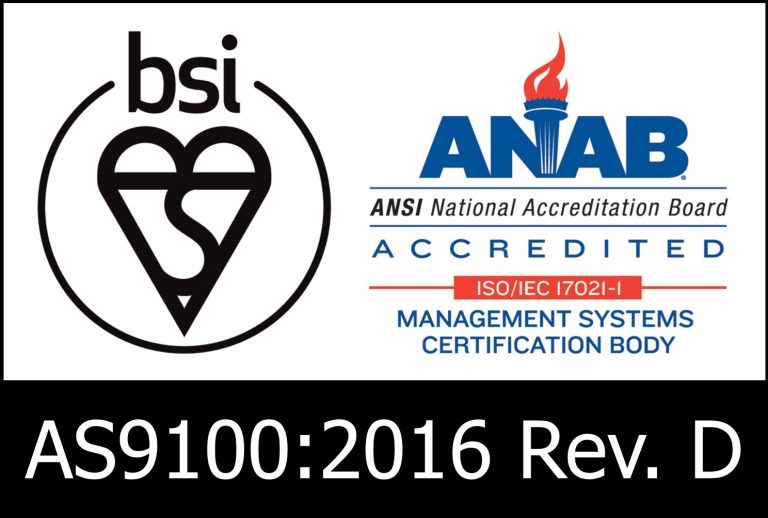
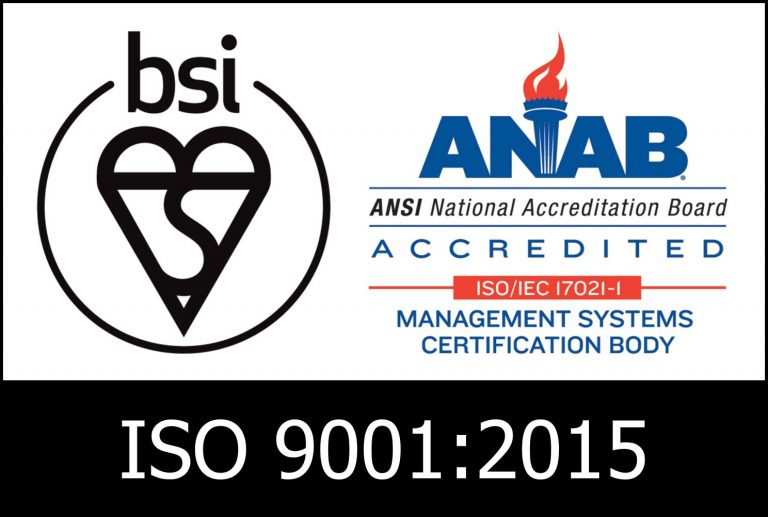
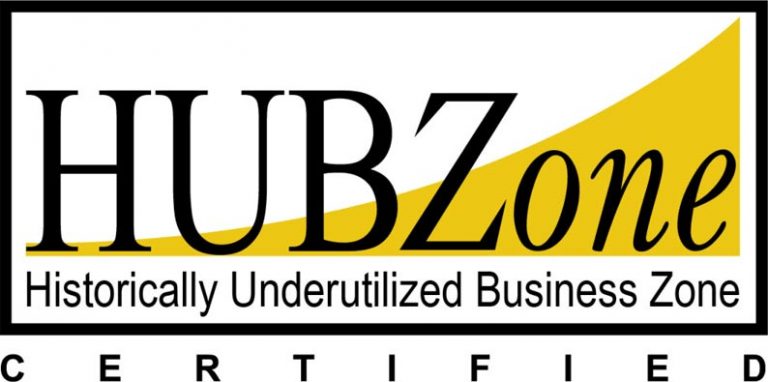
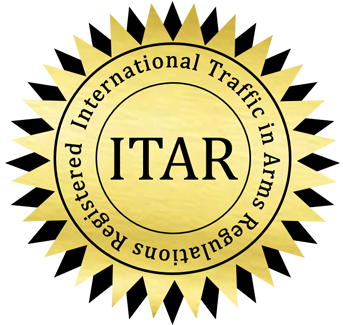
At-A-Glance Benefits of ADM’s Metal Injection Molding Services
- Custom metal injection molding with a wide variety of metal feedstocks including stainless steel, tool steels, copper, tungsten, and more
- Injection molding of single-cavity and multicavity molds
- 110-ton metal injection molding press
- 1.9-ounce shot size
- 2.7-ounce shot size
- 3.7-ounce shot size
- Product Design Assistance
- Design for Manufacturability (DfM) Feedback
- Material selection and validation
- Prototyping
-
Performance and management of value-added secondary operations, including:
- Post-processing operations in our high-precision machine shop
- Ink pad printing
- Labeling
- Heat treating
- Plating
- Anodizing
- Debinding
- Sintering
- Machining
- Product assembly
- Packaging
- Warehousing
- Shipping
- Strict quality inspections to meet or exceed the quality requirements for all products and processes.
- 24/7 operations capability to meet customers’ demands
- In-house collaborative personnel who thoroughly understand the highly interdependent processes of mold building and injection molding to provide what most companies cannot — a true one-stop shop for precision injection molded parts